Brake Pad Failures and How To Avoid Them

Brakes are important as we all know, but let’s have a look at why and how brakes fail…
There are;
- Total failures
- Lack of performance
The first total failure cause and the most common factor is pad wear. Brake pads do wear out by design and this can happen anywhere from 6000 miles on certain heavy SUVs to as high as 50,000. As brakes wear, modern systems will give either a dash light warning or an audible screech to alert the driver. A good tip is to change pads when about half worn as life, after this amount of pad thickness loss pad wear accelerates anyway. The lower half of the pad wears 3-5 times as fast as the first half when the pads were new.
Corrosion is also a big factor in pad safety. With constant exposure to moisture, road salt, and tyre spray corrosion sets in especially on rear brake pads where the near kerbside pad gets huge amounts of road splash and is constantly getting wet and then drying out under braking. This constant “steam cleaning” of the pads can cause interlayer corrosion between the pad compound and the steel backplate and cause the total pad to debond.
EBC brakes recognised this problem a decade ago and made two rapid-fire changes to its pads to prevent this. The first change was to include alkaline anti-corrosion additives into the pad mixes which drastically reduced interlayer corrosion. Back in 2011 EBC built its own pressworks at its Northampton HQ and installed two massive presses to apply the patented Nucap Canada NRS system to its backing plates. At a cost of over a million pounds, this was no small step for safety purposes and added significant costs to the price of the product but any and all pad debond failures completely went away. EBC backing plates for all its organic motorcycle and automotive pads are now made this way for many years.
This is what an NRS backing plate looks like.
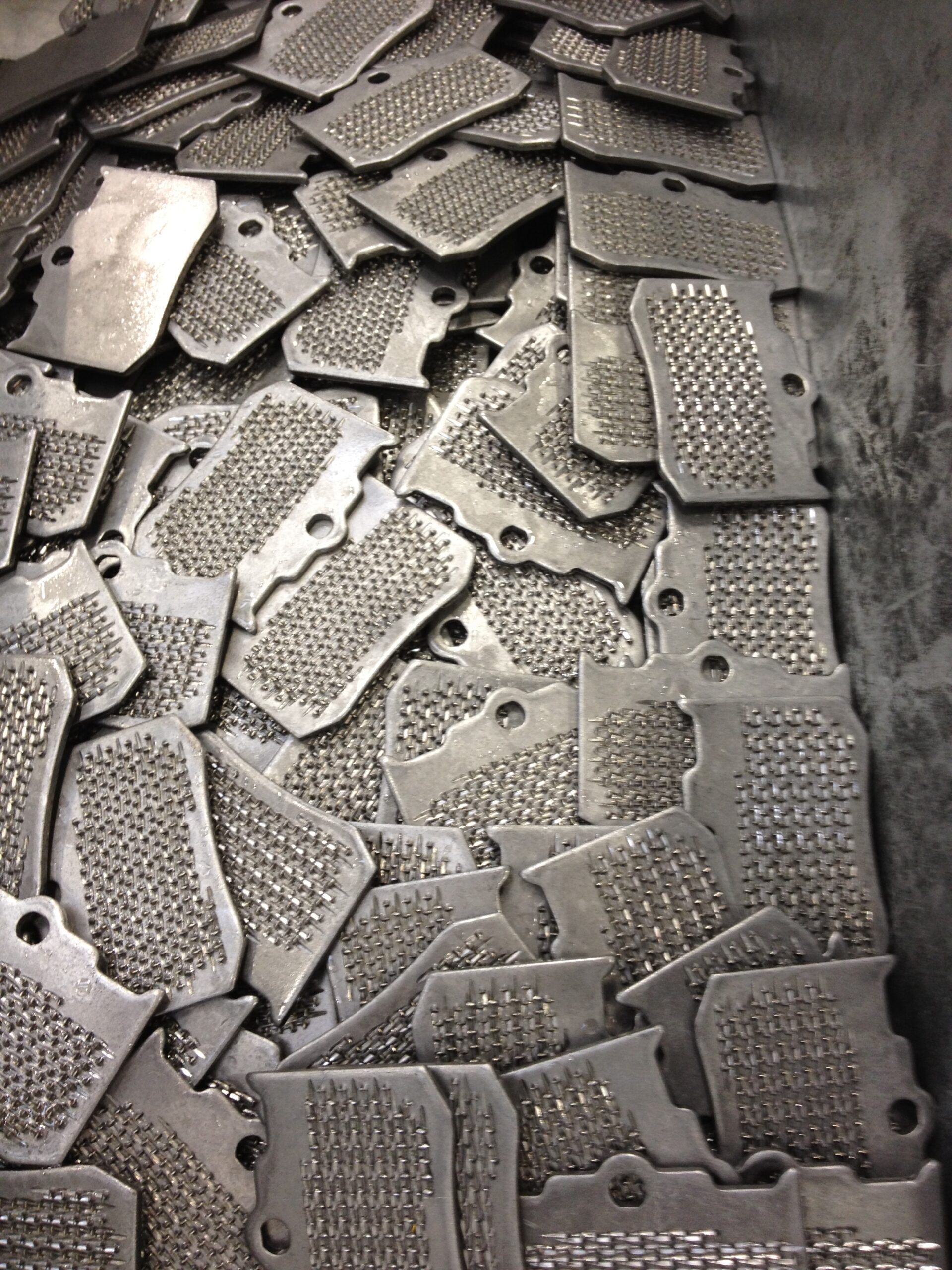
Leave a comment